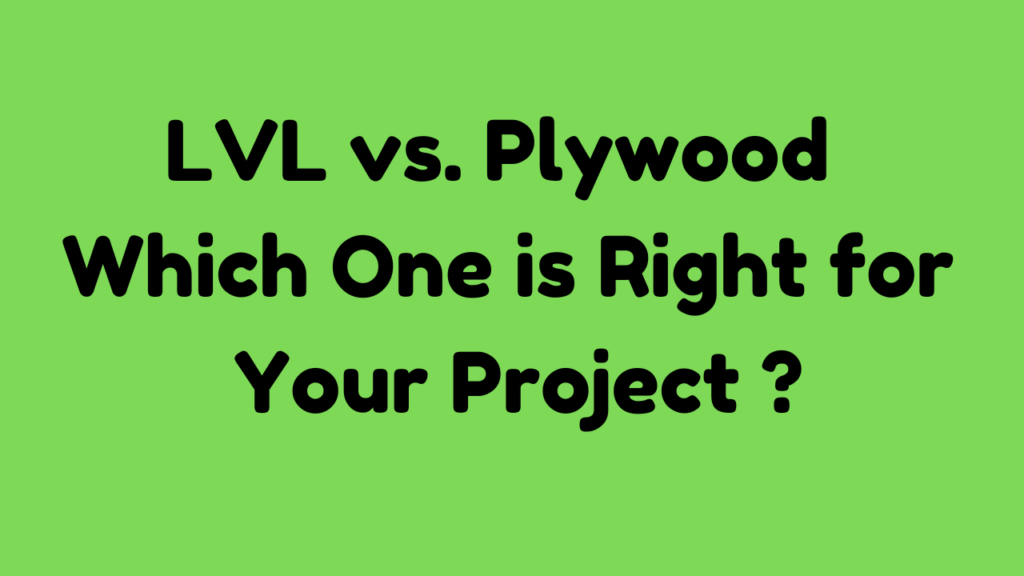
When picking the right material for building, woodworking, or DIY projects, it’s important to know the differences between laminated veneer lumber (LVL) and plywood.
Each has its own strengths and is best for different jobs. In this article, we will explain how LVL and plywood are different, their benefits, costs, impact on the environment, and the best ways to use them.
What is Laminated Veneer Lumber (LVL)?
Laminated veneer lumber (LVL) is a type of engineered wood. It is made by gluing thin layers of wood together. These layers are pressed and heated to create a strong and stable material. LVL is mainly used for building structures like beams, headers, and columns because it is very strong.
How is LVL Made?
LVL is made from thin wood layers, usually from fast-growing softwood trees. First, the wood is peeled into thin sheets and dried. Then, these sheets are glued together with a strong adhesive.
The layers are arranged so that the wood grain runs in the same direction. This makes LVL stronger and more stable than solid wood. The adhesive also removes natural flaws in the wood, making LVL more reliable.
Types of Laminated Veneer Lumber
There are several grades and sizes of LVL, designed for different applications. The most common grades include:
Standard LVL: Typically used in framing, flooring, and as beams or headers.
High-strength LVL: Used for applications that require greater load-bearing capacity, such as in large beams.
Moisture-resistant LVL: Designed for environments exposed to high humidity.
Each type is tailored to specific structural needs, ensuring that you can select the right LVL for your project.
What is Plywood ?
Plywood is a type of engineered wood, but it is different from LVL in how it is made and used. It is created by gluing thin layers of wood together. The grain of each layer is placed in the opposite direction of the one below it.
This cross-grain design makes plywood strong and helps prevent warping.
How is Plywood Made ?
Plywood is made by stacking thin wood layers, called plies, on top of each other. These layers can be from hardwood or softwood. A strong adhesive bonds them together, with each layer’s grain running in the opposite direction.
This process, called cross-lamination, makes plywood strong, flexible, and less likely to crack or warp compared to solid wood.
Types of Plywood
There are several types of plywood, based on the wood species used and the intended application:
Softwood Plywood: Typically made from fir, pine, or spruce, used for structural applications.
Hardwood Plywood: Made from deciduous trees like oak and maple, used for cabinetry and fine woodworking.
Marine Plywood: Highly water-resistant, used in environments exposed to moisture, such as boat building.
Each type serves specific purposes, from heavy-duty construction to delicate furniture making.
Key Differences Between LVL and Plywood
Material Composition
The main difference between LVL and plywood is how the wood layers are arranged. LVL has all its layers facing the same direction, making it very strong for carrying heavy loads.
Plywood has layers with grains going in different directions, which helps it stay stable and resist warping but does not make it as strong in one direction.
Construction and Production Differences
LVL is made with thicker and longer wood layers, making it perfect for heavy-duty jobs like beams and headers. Plywood, with its alternating layers, is more useful for general building projects like walls, floors, and furniture.
Durability and Strength
LVL is stronger than plywood and can support more weight over long distances. This makes it great for structural uses. Plywood is also strong but more flexible, which makes it better for projects that need bending or shaping, like curved walls or cabinets.
Applications of Laminated Veneer Lumber (LVL)
Framing and Beams
LVL is widely used in construction, especially in framing applications where long, straight beams or headers are required. It is often used for load-bearing structures like walls, ceilings, and roofs.
Furniture Making
LVL is also used in furniture design, particularly for high-strength applications like tables, shelving units, and custom furniture pieces. Due to its strength and versatility, LVL is becoming more popular in both industrial and residential furniture making.
Also read: OSB vs Plywood: 8 Differences You Need to Watch Out For
CDX vs OSB: Which One Is the Best for Your Next Project?
Applications of Plywood
Wall and Roof Sheathing
Plywood is most commonly used in construction as a sheathing material for walls, roofs, and floors. It’s highly durable, easy to work with, and provides structural support in these applications.
Decorative Projects
Because of its versatility and aesthetic appeal, plywood is often used in furniture making, cabinetry, and interior decor. Plywood’s smooth surface makes it ideal for veneer finishing and painting, allowing for beautiful custom finishes.
Cost Comparison
When considering cost, plywood is generally less expensive than LVL. The difference in price is largely due to LVL’s higher strength and specialized production process.
However, the cost of LVL may be justified in situations where higher strength or more precise dimensions are needed, reducing the amount of material waste or time required for framing and structural work.
Which is Better for Specific Projects ?
Choosing LVL for Structural Projects
For large-scale framing, beams, or any application that demands high strength over long spans, LVL is the material of choice. It excels in structural integrity and load-bearing capabilities.
Choosing Plywood for Finishing and Design
Plywood is ideal for projects where appearance matters, such as cabinetry, furniture, or decorative wall finishes. It offers a versatile, cost-effective solution with an easy-to-finish surface.
Frequently Asked Questions (FAQs)
Is LVL stronger than plywood?
Yes, LVL is stronger because all its layers go in the same direction, making it great for heavy loads.
Can LVL replace plywood?
LVL can be used for some of the same purposes, but it’s not ideal for decorative or lightweight uses.
How is LVL made?
Thin wood layers are glued together with the grain in the same direction, then pressed with heat to make a strong material.
Which is cheaper, LVL or plywood?
Plywood is usually cheaper, especially for non-structural uses like cabinets. But LVL can be cost-effective for strong structural needs.
Can plywood hold heavy loads?
Plywood can support weight, but it’s not as strong as LVL. It’s better for flexible or decorative projects.
Which is better for the environment?
Both are eco-friendly because they use thin wood layers from sustainable sources. LVL may create less waste.